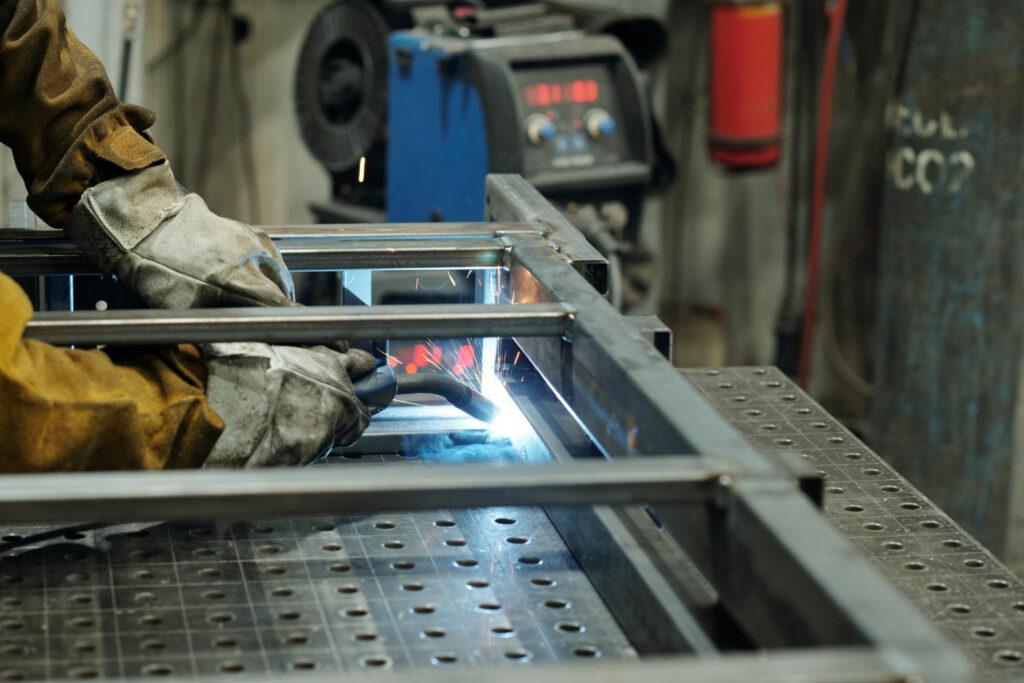
Surface treatment, also known as surface finishing or surface engineering, is a critical step in many manufacturing processes that involves modifying the surface of a material to enhance its properties and performance. It’s about altering the material’s outermost layer without affecting its overall bulk characteristics.
Why is surface treatment important?
Surface treatment plays a crucial role in improving a product’s functionality, durability, and aesthetics.
- Improved Adhesion: Surface treatments can create a bondable surface, crucial for applications like coating, painting, and joining different materials.
- Enhanced Performance: They can significantly boost material performance by improving properties like wear resistance, corrosion resistance, and conductivity, leading to increased lifespan and reliability.
- Increased Durability & Resistance: Surface treatments can make materials more durable and resistant to abrasion, chemicals, high temperatures, and humidity, vital for components exposed to harsh environments.
- Desired Aesthetics: Surface treatments can enhance the product’s visual appeal by modifying its appearance, texture, and color through processes like polishing, coating, and finishing.
- Corrosion Protection: Treatments like plating and anodizing form protective layers that shield the metal from corrosive elements, extending its service life.
- Wear Resistance: Surface hardening treatments, like nitriding or carburizing, create a hard layer on the surface, reducing wear and tear.