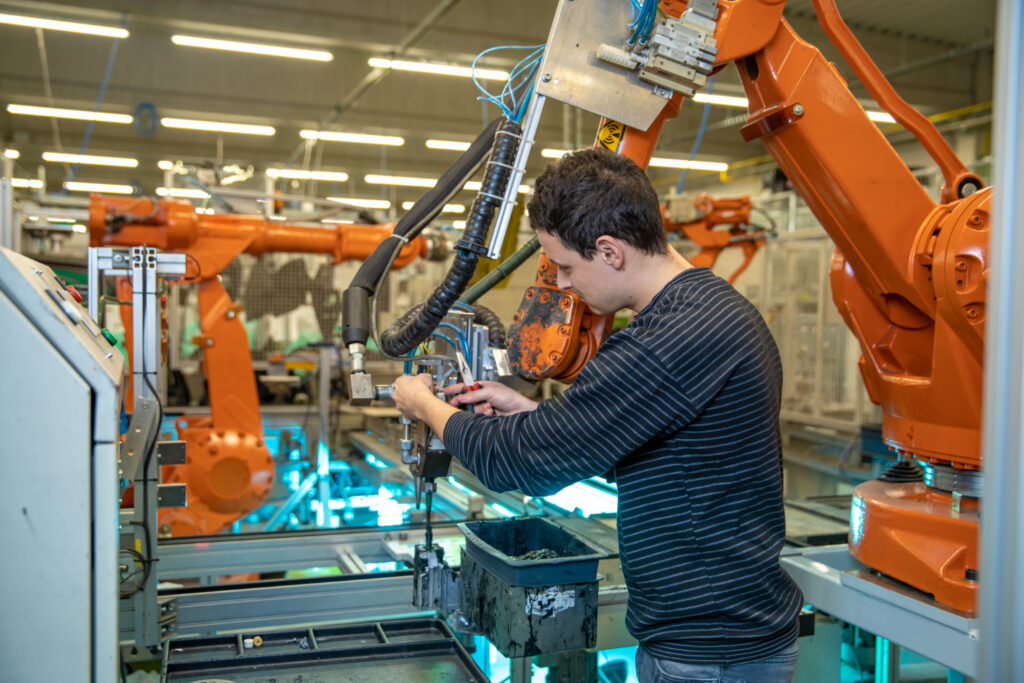
In the realm of manufacturing, the assembly section is the critical stage where individual components and parts are brought together and joined to create a complete and functional product. It is a pivotal part of the overall manufacturing process, transforming raw materials and fabricated components into the finished goods ready for the market.
Key elements of assembly in manufacturing
- Sub-assemblies: Complex products often involve sub-assemblies, which are smaller, self-contained functional units that are assembled independently before being integrated into the final product. Think of the engine of a car or the motherboard of a computer as examples of sub-assemblies.
- Joining methods: Components can be joined using various techniques, including permanent methods like welding, soldering, brazing, or adhesive bonding, or semi-permanent methods like screws, bolts, and other fasteners. The choice of joining method depends on the material, desired strength, and whether the components need to be easily separated.
- Tools and equipment: Assembly relies on a wide array of tools, ranging from basic hand tools like screwdrivers and wrenches to advanced machinery like robotic arms, conveyors, vision systems, and automated storage and retrieval systems (AS/RS).
- Workstations: Assembly lines are often designed with dedicated workstations where specific tasks are performed. These can be conveyor-based, with products moving from station to station, or fixed, where operators assemble components at a stationary point.
- Quality control: Ensuring the quality of the assembled product is paramount. Quality control measures are integrated throughout the assembly process, involving inspections, functional testing, measurements, and statistical process control (SPC) to identify and rectify defects early on.
- Different techniques are employed based on production volume, product complexity, and budget constraints. These include manual assembly, automated assembly using robots and machines, hybrid assembly combining both manual and automated tasks, and lean assembly focusing on reducing waste and improving efficiency.
Types of assembly lines
- Continuous flow assembly line: Used for mass-producing a single product, where materials and components move continuously through the line.
- Cellular assembly line: Produces batches of related products using a series of cells or workstations, each handling a specific task.
- Balanced assembly line: Workstations are arranged and tasks distributed to ensure efficient flow and prevent bottlenecks.
- Flexible assembly line: Designed to be easily reconfigured to accommodate variations in product design or production volume.
- Automated assembly line: Utilizes robotics and advanced technologies to automate assembly tasks.